Turnkey service
Capitol offers a turnkey service for zinc die cast parts. Our fully integrated, ISO 9001-2015 certified factory in Montreal, Canada handles everything from design of tooling to finished products. Our 100,000 square foot facility includes over 50 different processes and a hardworking team of people to get our customers exactly what they need, when they need it.
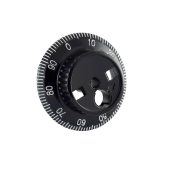
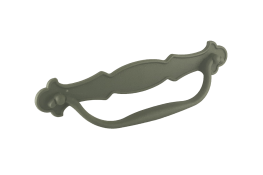
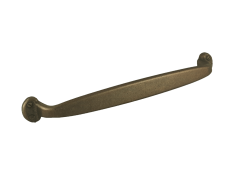
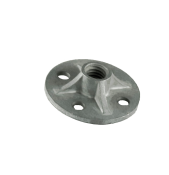
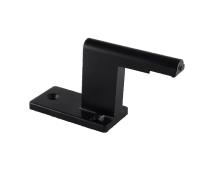
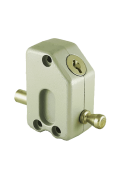
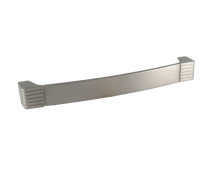
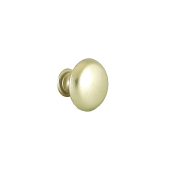
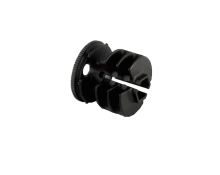
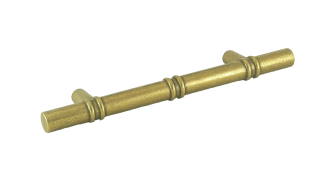
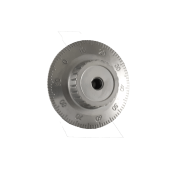
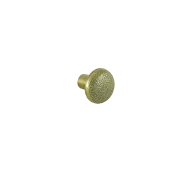
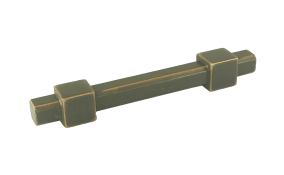
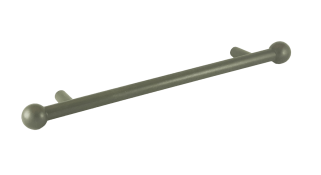
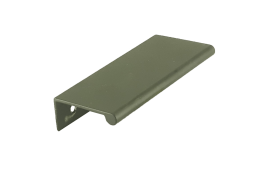
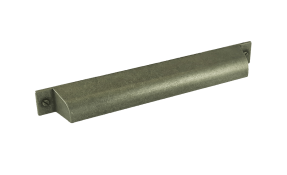
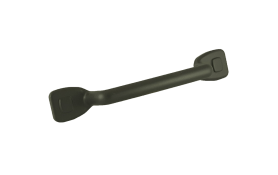
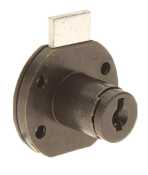
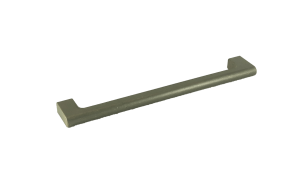
Why Zinc Die Casting?
Zinc die casting is the ideal manufacturing process for complex shapes requiring high strength, specific surface finishes, and repeatable dimensional accuracy.
Zinc alloy characteristics to consider when selecting a material for a component:
- Thin wall sections
- High production rates
- Minimal secondary machining required
- Smooth finishes possible
- High dimensional accuracy, strength
- Low in cost
- Fully recyclable
- With surface treatment, it is resistant to corrosion
- High availability of surface treatments
These are Zinc Alloys we work with
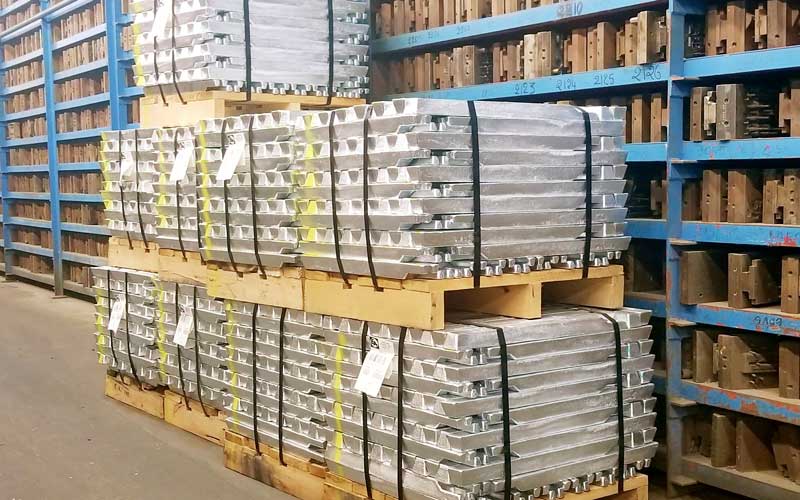
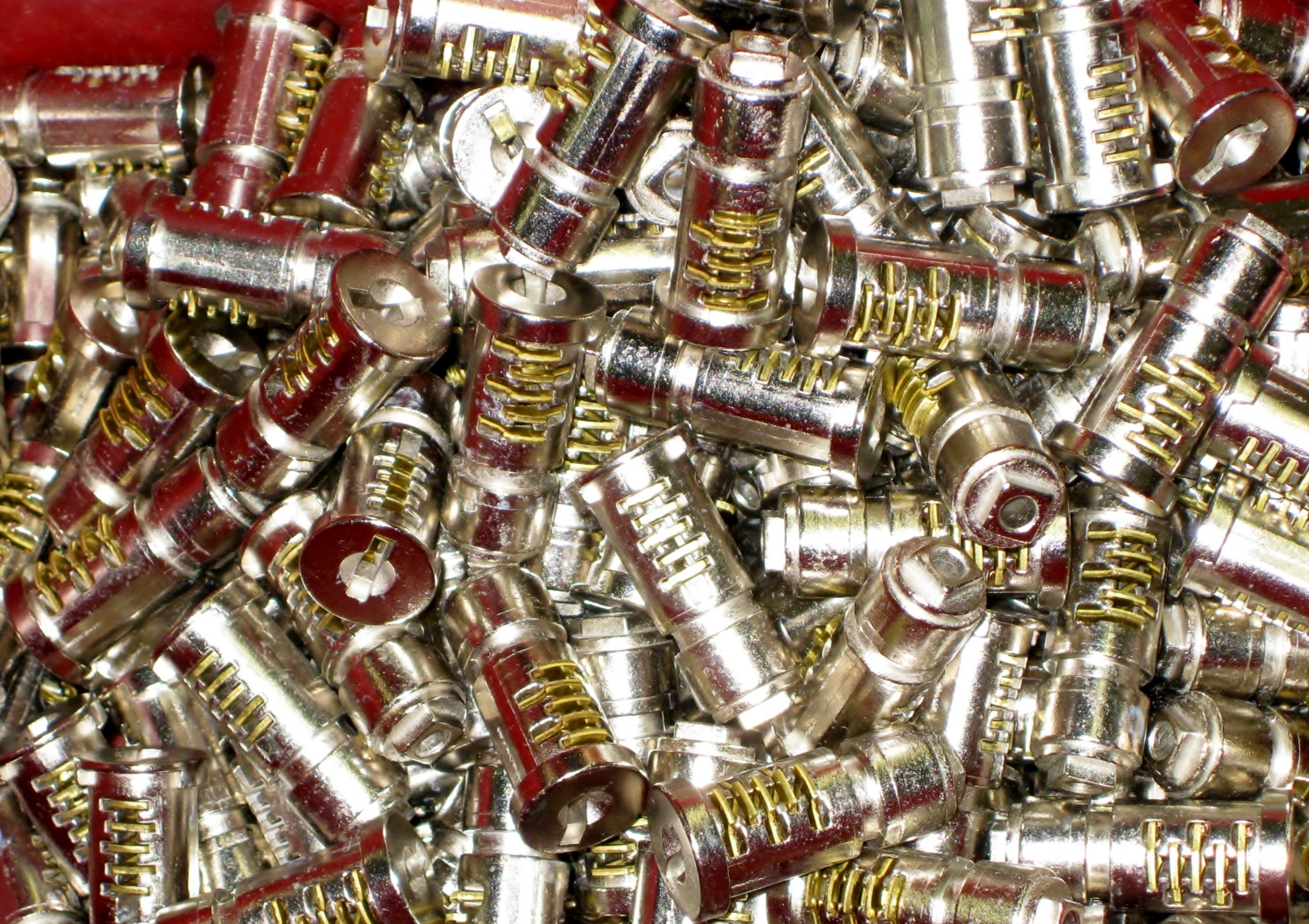
Industries
While we work with a multitude of industries and are always getting introduced to new challenges and industries, we have specialized in the following industries.
- Furniture Hardware
- Security Products
- Military
- Consumer Goods
Capabilities
Our expertise in zinc die casting doesn’t end with die casting itself. We have over 50 processes to finish the die cast parts and deliver a finished product, or a component ready for assembly. Our Capabilities include:
- Tooling Design
- Die Casting
- Secondary Machining
- Surface treatments
- Powder-coating
- Relieving/Sanding
- Lacquering
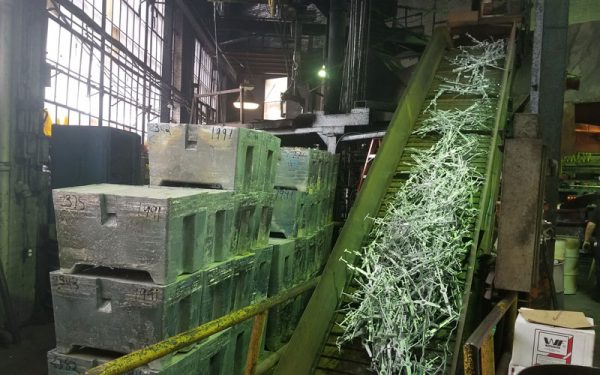
Lean Manufacturing
With our Lean Thinking approach to manufacturing, we have minimized waste, inventory and work-in-progress. An estimated 90% of our weekly production is shipped to our customers by the end of a 5-day week, with the remaining 10% of the week’s production being used to fill up processes at the beginning of the following week.
This approach allows us to manufacture on-demand and offer just-in-time delivery, with a typical lead time of 1-2 weeks, making Capitol practically an extension of our customers’ factories.
Our approach has also led us to streamline machine setups, eliminating the need for large production runs and high MOQs. While lean manufacturing principles were applied originally to save costs on our part, it has ultimately resulted in benefits for our customers, such as cost savings, low MOQs, short lead times, added flexibility in purchasing, lower inventory carrying costs, and the resulting increased cash-flow.
Our Process
The process always begins with a request for a quote, or inquiry. Our engineers will then analyze the part/s to be produced, based on customer requirements and technical drawings. If any changes are recommended for the die casting process, they will be suggested to the customer.
The process always begins with a request for a quote, or inquiry. Our engineers will then analyze the part/s to be produced, based on customer requirements and technical drawings. If any changes are recommended for the die casting process, they will be suggested to the customer. Ultimately, we will finalize a component design that will satisfy both the customer’s needs and our process requirements. If possible, samples/prototypes are made for approval and validation, using 3D printing, sand casting, spin casting, or CNC machining.
In this phase, our industrial engineers also determine how the component will be processed through our factory, ensuring that the end result will bare all the specifications of the customer, including dimensional integrity and aesthetic appearance
Once a design has been approved by the customer, we move on to tooling design, where our engineers find the most cost-effective way to produce the component, minimizing secondary operations, if possible, and ensuring the tool will be easy to maintain throughout its lifetime.
The final phase of the process is the production in large scale. Our QC department is involved right from the beginning, working closely with our machine operators to ensure the “first off” is duly checked for any inconsistencies or deviations from the expected dimensions and tolerances, any possible porosity in the components coming off the die casting machines (if applicable), and verifying that the surface finish is adequate for subsequent processes and surface treatments.
Once a “first off” is approved, regular spot checks are performed throughout the production run to confirm the repeatability of each process.